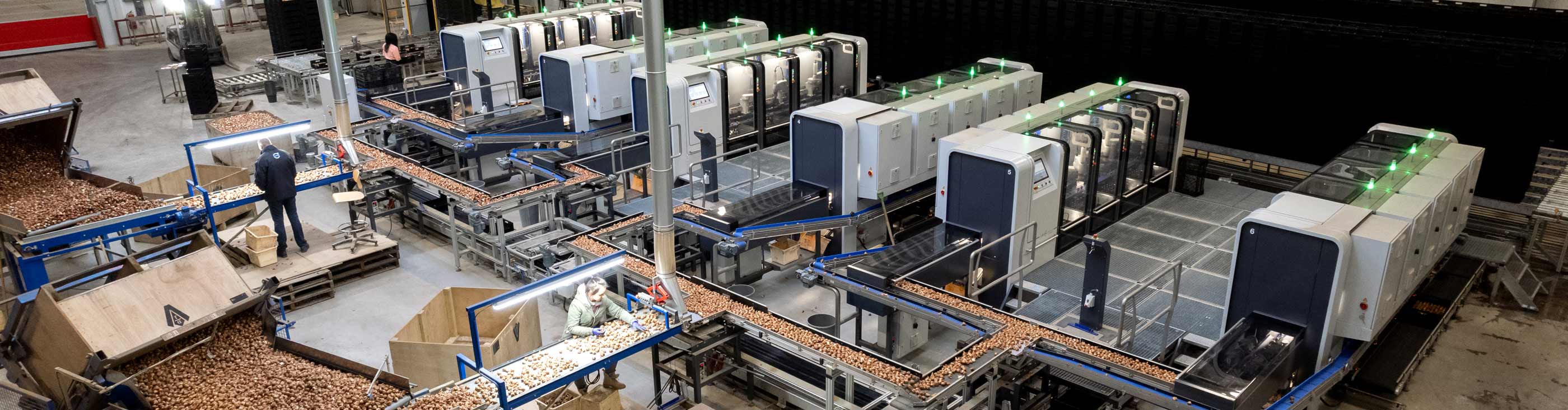
Geautomatiseerd proces voor het modulair verpakken van tulpenbollen.
ISO, Horti Innovators, automatiseert complexe en hoog-cyclische processen in de land- en tuinbouw met de hulp van robotica, vision, AI en machine learning. Een belangrijke doelgroep vormen de kwekers van tulpenbollen. SMC’s communicatieoplossingen helpen kwekers om ongekende aantallen tulpenbollen te sorteren en in de prikbak te plaatsen. ISO koos hierbij voor een draadloze communicatieoplossing van SMC die niet alleen uiterst betrouwbaar is, maar waarmee het bedrijf bovendien een aantal complexe ontwerpproblemen kon oplossen.
Het opplanten van tulpenbollen is een complex proces. Het gaat namelijk niet alleen om zeer grote aantallen, maar de bollen dienen ook nog eerst in een rij met bepaalde tussenafstanden te worden gelegd. Daarbij dient iedere individuele tulpenbol bovendien met het spruitje (het eerste begin van de stengel van de tulp) omhoog te worden geplaatst. Een extra complicatie is dat de tulpenbol bovendien zodanig in de prikbak vastgezet dient te worden dat de bol ook tijdens transport van de prikbak in de juiste positie blijft staan. Dit is cruciaal om te voorkomen dat de spruit beschadigt.
ISO heeft een modulair opgebouwde bollenplantsysteem ontwikkeld waarmee dit gehele proces kan worden geautomatiseerd. Robots en camera’s kunnen hierdoor vrijwel alle taken en handelingen op zich nemen. “Het gaat om standaard machines die configureerbaar zijn naar de layout en de specificaties van de klant. Iedere machine is in staat om alle soorten en maten tulpenbollen voor snijbloemen te verwerken”, zegt Bastiaan Ophorst, mechanical engineer bij ISO.
Slimme procesgang vereist draadloos visionsysteem
Hoe werkt deze bollenplantmachine? Vorkheftrucks voeren de tulpenbollen in kuubse bakken aan. De bollen zijn dan al op maat gesorteerd. De grootte van de bol bepaalt namelijk welke bakken voor het opprikken gebruikt moeten worden. De kuubse bak wordt geleegd in een verzamelbak aan het begin van de lijn. De tulpenbollen komen hier enkele lagen hoog in terecht. Om te komen tot een nette rij van bollen die door de grijpers van de robotarmen kunnen worden opgepakt, worden de bollen door middel van trilplaten in de richting van het laadstation getransporteerd. De trilplaten zorgen ervoor dat de meerdere lagen met tulpenbollen worden teruggebracht tot een enkele rij. Ook zorgen de trilplaten ervoor dat er ruimte tussen de individuele bollen ontstaat. Deze tussenruimte is afhankelijk van het aantal bollen dat in prikbakken geplaatst dient te worden.
Hierna maken zes camera’s een beeld van iedere individuele tulpenbol. Deze zes beelden worden samengebracht tot een 3D-beeld. Daarmee is duidelijk wat de positie van iedere bol is op de band, wat de 3D-geometrie van de bol is en waar het spruitje zich bevindt. Deze informatie samen bepaalt hoe de grijper straks iedere individuele bol dient op te pakken. Ook vindt via de 3D-camera een optische health check plaats van iedere bol om te voorkomen dat per ongeluk een ongezonde bol wordt opgeprikt. Deze zogeheten ‘zure bollen’ worden niet door een grijper gepakt, maar worden door het besturingssysteem van de machine gemarkeerd en aan het einde van de band verwijderd. De snelheid van de band kan worden gevarieerd om de gewenste tussenruimte tussen de bollen te realiseren. Hiermee kan bovendien stuwing in de machine worden voorkomen.
Nadat de camera’s en het visionsysteem de positie en de oriëntatie van de bol op de band hebben bepaald, worden de bollen met de vereiste tussenruimte in een nette rij de bollenplantmachine ingevoerd. Deze lijn bestaat in de regel uit meerdere modules (zogeheten ‘opplantmodules’), meestal gaat het om vier modules. Iedere module heeft één robotarm. De informatie over de positie en de oriëntatie van de bol bepaalt nu hoe de grijpers van de robotarmen een reeks van bollen oppakken en plaatsen op een zogenaamde steekbrug. Het aantal posities op de steekbrug is afhankelijk van het aantal bollen dat in één rij in de prikbak kan worden geplaatst. De robotarm plaatst de bollen nu zodanig op de steekbrug dat iedere bol precies in een grijpertje wordt geplaatst. Iedere steekbrug telt maximaal twee keer zeven grijpers die in twee parallelle rijen 180 graden tegenover elkaar staan opgesteld. Als zeven grijpers gevuld zijn, roteert de steekbrug en wordt de rij met bollen in de prikbak geplaatst. Afhankelijk van het type bol bevindt zich in de bodem van de verpakking een klein pinnetje per positie voor een tulpenbol. Massa wordt gekweekt op waterbroei, de exclusievere soorten op grondbroei. De steekbrug drukt de bollen zachtjes op dit pinnetje of in de aarde, zodat de positie van de bol wordt gefixeerd. Hierdoor blijven de bollen ook tijdens transport met de spruitjes omhoog gepositioneerd. Is de prikbak vol, dan wordt deze uit de module bewogen en wordt diens plaats ingenomen door een nieuwe lege prikbak. De met bollen gevulde prikbak of prik-tray wordt vervolgens naar een laatste station getransporteerd waar een medewerker van de kweker nog een laatste visuele check doet.
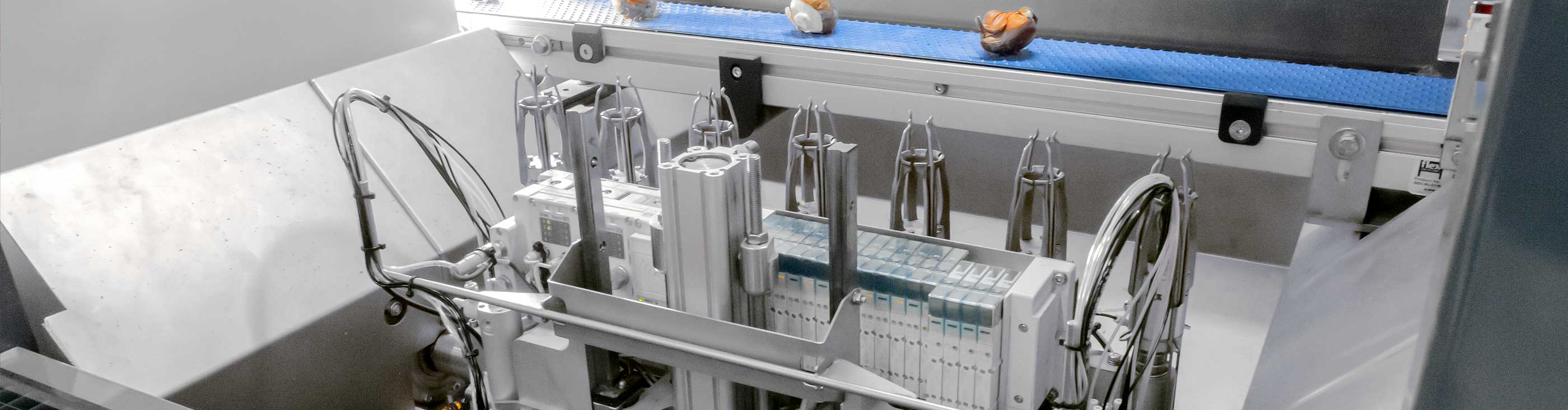
Positionering van de bollen op de steekbrug.
Betrouwbare draadloze communicatie gerealiseerd
ISO stond bij het ontwerpen van deze bollenplantmachine voor een belangrijke technische uitdaging: de roterende beweging van de steekbruggen. Deze rotatie verloopt namelijk altijd in dezelfde richting. Er dient echter communicatie plaats te vinden tussen de centrale besturing van de bollenplantmachine, de robotarmen en de steekbruggen. Door de roterende beweging was een bekabelde oplossing erg lastig te realiseren. Ophorst legt uit: “We hebben gekeken naar het gebruik van sleepringen, maar dat zou erg veel contacten hebben vereist. Er zitten meer dan dertig functies/detecties in iedere steekbrug. Dat is via bedrading niet te doen. Daarom waren we er al snel van overtuigd dat we voor draadloze communicatie moesten gaan. Maar hoe doe je dat op een betrouwbare manier?”
“De oplossing kwam van SMC”, vertelt Bert Evertse, PLC-programmeur bij ISO en verantwoordelijk voor de besturing van de bollenplantmachine “We hadden al wat testen uitgevoerd met een product van een ander merk, waarbij de communicatie via Bluetooth verliep. Dat bleek behoorlijk storingsgevoelig en dat is - zeker bij dit soort highspeed-lijnen - zeer ongewenst. SMC kwam echter op precies het goede moment met de juiste oplossing. Wat SMC ons als oplossing voorstelde, is een industrieel draadloos netwerk binnen de bollenplantmachine. Op het niet-roterende deel van de lijn hebben we nu een base-module geplaatst, op de steekbrug een remote module. Data voor het aansturen van de steekbrug worden hierbij via SMC Industrial Wireless Communication van de base naar de remotes gestuurd. De besturingsdata - het gaat om circa 60 bits per module plus wat data voor diagnosedoeleinden en dergelijke - worden naar de zender gebracht via een seriële communicatie (Ethernet/IPTM). De configuratie van de base en de remote wordt bij installatie eenmalig geadresseerd via NFC (Near Field Communication).”
De afstanden tussen de base-module en de remote-modules kunnen variëren. Afhankelijk van het aantal modules waaruit de bollenplantmachine bestaat, is dat 5 à 6 meter. Maximaal is een straal van 10 meter mogelijk. De bewegende delen in iedere module - denk aan de servomotoren van de robotarmen - blijken geen enkele invloed te hebben op de datatransmissie. “Van storingen is absoluut geen sprake", vertelt Evertse. “Sterker nog, de communicatie is uiterst betrouwbaar.”
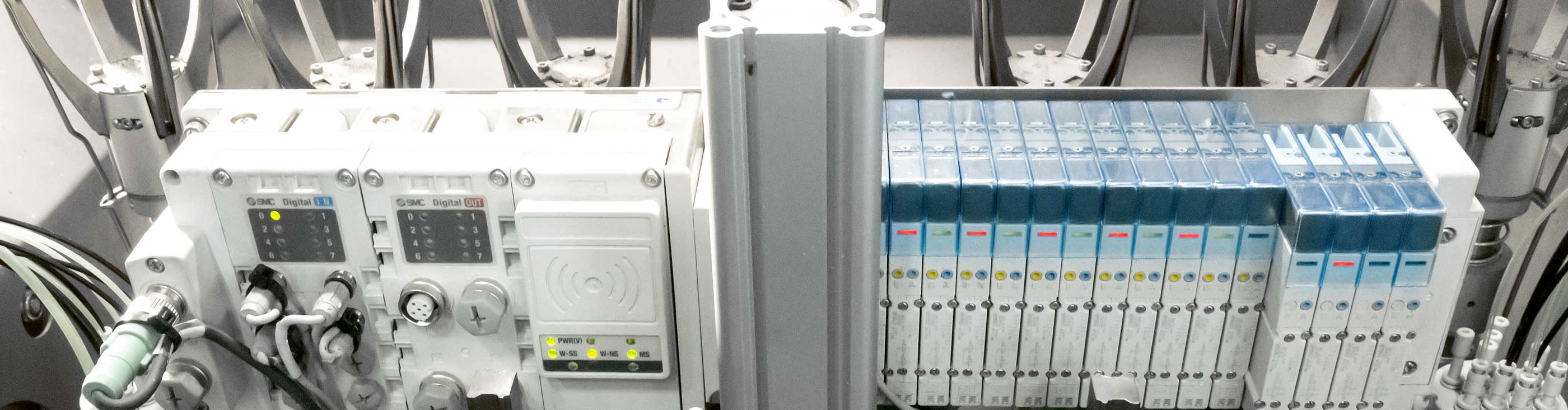
Draadloze externe module op de steekbrug.